BuySellBA
Administrator
3D printed homes: a technology that could transform the housing deficit in Argentina - Infobae
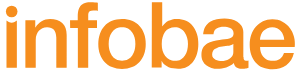
Source:

Viviendas impresas en 3D: una tecnología que podría transformar el déficit habitacional en Argentina
Promete ser más económica, rápida y sostenible que los métodos tradicionales. Cuáles son los materiales empleados, los costos estimados y las posibilidades de implementación en el país

January 26, 2025
It promises to be cheaper, faster and more sustainable than traditional methods. What are the materials used, the estimated costs and the possibilities of implementation in the country?
By Jose Luis Cieri
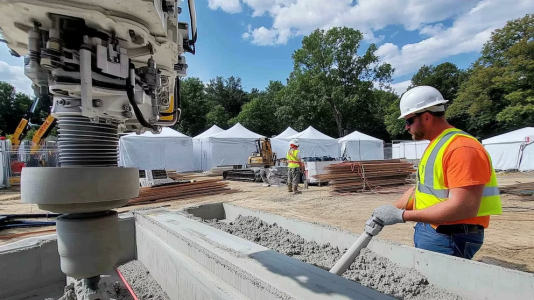
According to experts, building a 70 m2 house with 3D printing takes only 60 hours (Illustrative Image Infobae)
Architecture is making steady progress in the technological field, with innovations that are constantly surprising. 3D printing is gaining ground and promises to revolutionise the world of construction, with a 50% reduction in lead times and a faster, cheaper and more sustainable alternative to traditional methods.
Although it still faces challenges in countries like Argentina, experts and architects agree that its implementation could mean an important solution to the country's housing deficit, which is estimated at 3.5 million homes. This technological advance opens the door to a paradigm shift in the sector.
This technology allows the use of special concretes with polymers and fibers that, combined with water, achieve high resistance and printing speed.
It promises to be cheaper, faster and more sustainable than traditional methods. What are the materials used, the estimated costs and the possibilities of implementation in the country?
Furthermore, according to the manager of Sika's concrete division, César Gómez , this method "eliminates the need for traditional formwork, reduces construction times and generates less waste."
A complete 70-square-meter home can be printed in just 60 hours. Afterwards, the necessary finishing touches must be applied until construction is complete.
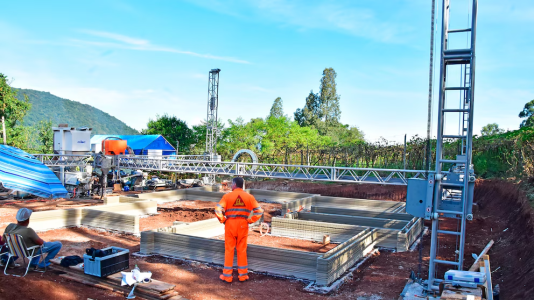
3D printed buildings generate less waste and carbon emissions (Photo Courtesy: Sika)
In fact, there are countries where entire neighborhoods were built using 3D printers, such as in Austin, Texas, as reported by Infobae . It's quite a challenge in Argentina, which raises the question: would you dare to live in a house like that?
Economic and environmental benefits
Homes built with 3D printers offer a number of economic and environmental advantages.They can be built on empty land, on pre-existing structures if they can support the loads, or on multi-story buildings, depending on the project.
Myriam Heredia , an architect and specialist in the subject, explained that this technology “reduces costs by optimizing materials and reducing waste.”
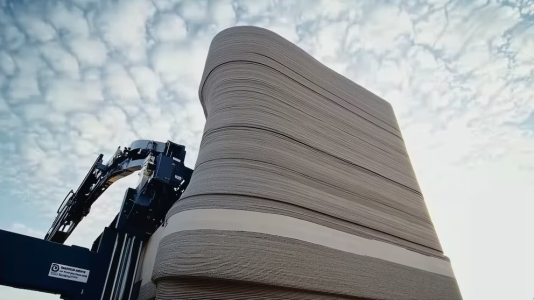
They have futuristic shapes (Illustrative Image Infobae)
An industrialized housing project could be completed in 6 to 8 months, compared to the two to three years required for traditional construction.
“In addition, Heredia said, “by reducing the energy used in construction and emissions linked to transportation, the carbon footprint is reduced.”
3D printing in construction stands out for its sustainability by using recycled or biodegradable materials, such as concrete with recycled additives.
Guillermo Tella , architect and doctor in Urban Planning, highlighted that this methodology “could allow for the design of housing solutions adapted to the needs of different urban communities, would optimize resources and would lead to the construction of more sustainable homes.”
Another vital aspect he highlighted is how this technology can help reduce costs not only in construction, but also in operation, thanks to more energy-efficient designs.
Specific challenges
The Argentine context poses specific challenges for the adoption of 3D printing in construction.According to Heredia, “implementation in the country depends on factors such as the availability of technology, private incentive policies and government regulations.”
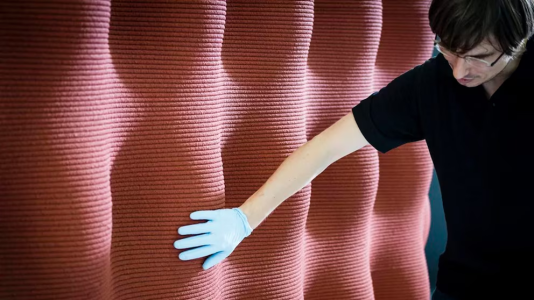
With wavy reliefs created by the points of the 3D printers during construction
Although it is estimated that mass adoption could occur within 5 to 10 years, the lack of trained professionals, along with high initial costs, keeps its progress difficult.
In Tella's words: "The problem of the housing shortage cannot be solved simply by building more housing, but we must also rethink how it is built."
This requires an adapted regulatory framework that encourages public-private collaboration and allows for testing new alternatives through pilot projects. These initiatives, he stressed, are key to overcoming cultural and social resistance to the use of these industrialized methods.
However, the projections are promising. Peripheral urban areas of cities such as Buenos Aires, Córdoba and Rosario are ideal for 3D printing projects due to their scale and high housing demand. Intermediate cities such as Mendoza, Tucumán and Neuquén are also viable, as they could benefit from their lower density and need for quick housing solutions.The problem of housing shortage is not solved just by building more houses, but we must also rethink how they are built (Tella)
In terms of climatically extreme regions, Patagonia and Cuyo are clear examples where the speed and adaptability of this technology can make a difference, especially in cold or arid areas.
Heredia highlighted that the areas with the greatest viability, both in terms of accessibility and temperate climates, include the Humid Pampas.
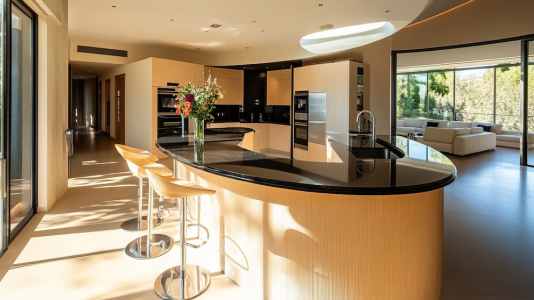
They are minimalist and designed with large windows to maximize the entry of natural light. It improves energy efficiency by reducing the need for artificial lighting, and creates larger and more comfortable spaces (Illustrative Image Infobae)
“However, extreme climates also offer unique opportunities. The speed of the system could be crucial in areas such as La Rioja, where traditional construction is more challenging, or in Patagonia, which has made considerable progress in the adoption of rapid construction technologies. It is especially suitable for regions with a high housing deficit such as the province of Buenos Aires, Santa Fe and Córdoba, which account for 50% of the problem in Argentina,” added Myriam Heredia.
Comparison of costs and methods
In economic terms, 3D construction costs are significantly lower than traditional methods.According to Heredia, while a home built using conventional techniques costs between USD 900 and USD 1,600 per square meter, one built using 3D printing could reduce those costs to a range of between USD 300 and USD 600 per square meter.
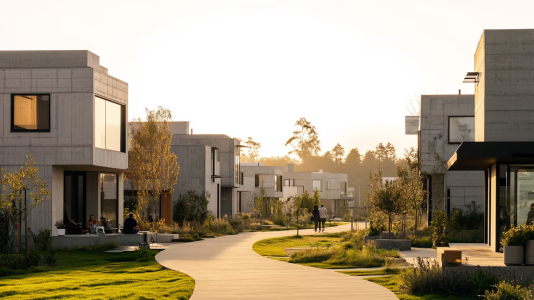
They can also be built on two floors (Illustrative Image Infobae)
This represents a 70% saving in direct comparison, although external and internal finishes usually represent an additional cost.
César Gómez reinforced this vision, stating that “automation reduces the need for intensive labor and allows work even at night, maximizing productive efficiency.”
Furthermore, the finishes of the rooms and exteriors can be adjusted in a traditional way to guarantee thermal insulation, habitability and durability.In other countries, a 70 m2, 3-room home usually sells for more than USD 60,000.
3D house facades are often minimalist and designed with large windows to maximize the entry of natural light. This not only improves energy efficiency by reducing the need for artificial lighting, but also creates larger, more comfortable spaces.
Step by step
Concrete 3D printing is a form of additive manufacturing that uses cement-based material to construct buildings, houses or components with shapes that were previously impossible or very difficult to achieve with traditional formwork.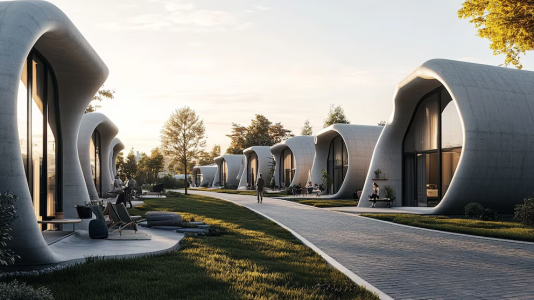
With original shapes (Illustrative Image Infobae)
Gomez said: “The micro concretes used consist of a cementitious powder with fibres and polymers, mixed with water at a specific station. In addition, an activator is added to the printing head which allows the setting time to be adjusted as needed. Colours can also be included to improve the aesthetics of the structures.”
With this type of materials, you get:
● High compressive strength.
● High printing speed.
● Adjustable setting time.
● Long open time for work.
● Ability to print at angles.
Towards a paradigm shift
The transition to more industrialized methods is not without its challenges. Heredia mentioned that, in the local context, “it will be crucial to achieve a sufficient scale of work that allows for the amortization of investments in machinery and technical training.”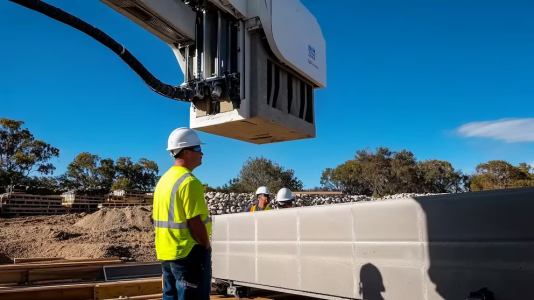
They are currently being built in different countries such as Belgium, Australia, the United States, China, South Africa, among others (Illustrative Image Infobae)
One barrier is the purchase of printers to make a 3D house, which are imported. If it is for applications for light prefabrication or mass-production units, the cost can vary. “However, as a reference, a printer intended for the construction of houses could have a base price of USD 200,000,” explained Gómez.
3D printing for homes automates almost the entire process, mixing and placing materials according to pre-designed patterns. Only personnel are required to install roofs, windows and doors.
These printers use cement and operate at minimum temperatures of 5°C, although they can work in climates as low as -35°C with adjustments such as thermal tents.
In Argentina, ensuring social acceptance means combining industrialized techniques with the integration of local labor, especially in government or social projects.
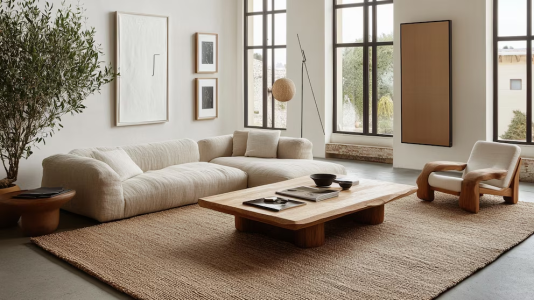
Interior finishings such as floors, paint and decoration, all products can be used as in other construction systems (Illustrative Image Infobae)
Guillermo Tella, for his part, stressed that this is a time of “break in traditional construction” and highlighted that, although 3D printing has limitations for large buildings, “its application in social housing and post-disaster reconstruction could make a difference.”
Public policies will be key, not only to resolve regulatory challenges, but also to foster collaboration between the private sector, universities and social organizations.
www.buysellba.com