BuySellBA
Administrator
Dry construction has more than 14,000 homes under construction: how it is built and what costs it has - Infobae
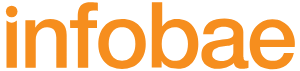
Source:

La edificación en seco tiene más de 14.000 viviendas en obras: cómo se construye y qué costos tiene
El steel frame no se detiene: la perfilería de acero permite acortar plazos. Una unidad de 70 m2 puede completarse en 6 meses; cuáles son los pasos clave

November 18, 2024
Steel frame doesn't stop: steel profiles allow for shorter deadlines. A 70 m2 unit can be completed in 6 months; what are the key steps?
By Jose Luis Cieri
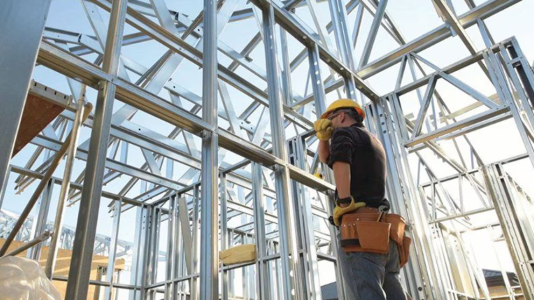
Steel frame construction is spreading in Argentina. It is a very resistant system and can withstand strong winds and challenging weather conditions.
The dry construction method, known as steel frame , is transforming the housing construction sector in Argentina. This system, which uses lightweight steel structures, has become a popular choice due to its versatility and efficiency, allowing both the construction of new homes and the expansion of existing ones.
It is estimated that more than 14,000 units are currently being built or expanded using this method in various regions of the country.
Mariana Stange , from Mariana Stange Real Estate, told Infobae that “the growing interest in steel frames is due to their numerous advantages over traditional methods. One of the main advantages is the efficiency in construction times, which translates into greater profitability and reduced financial costs, especially in inflationary contexts.”
Furthermore, as it is an industrialized system, it offers greater precision and a smaller margin of error, since many of its parts are mass produced, which guarantees quality and reduces waste.
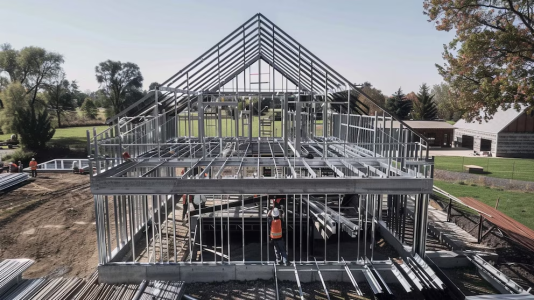
On a construction site of more than 70 m2, between 5 and 12 people can work between the start and completion of the house (Illustrative Image Infobae)
Another significant benefit of steel frame is its energy efficiency. Constructions using this system integrate thermal and acoustic insulation materials, which not only improve the comfort of the spaces, but also contribute to energy sustainability. This feature is especially relevant in a context of climate change and growing environmental awareness.
In addition to efficiency, the steel frame offers flexibility in design, allowing it to be adapted to different types of terrain and projects, as well as greater durability against adverse weather factors. These advantages position it as a competitive alternative in the real estate market, both for single-family homes and for larger constructions.
Expansion in Buenos Aires and Patagonia
Regarding the adoption of dry construction in the Autonomous City of Buenos Aires and Greater Buenos Aires, Mariana Stange highlighted that this system has become particularly popular in areas of residential expansion and in low and medium density neighborhoods . “Areas such as Tigre, San Fernando, Pilar, Villa Devoto and Parque Chas are experiencing growth in the use of this technique,” she said.Stange also stressed that in Patagonia, where extreme weather conditions require greater insulation, steel frames have proven to be an ideal solution to ensure thermal efficiency in homes.
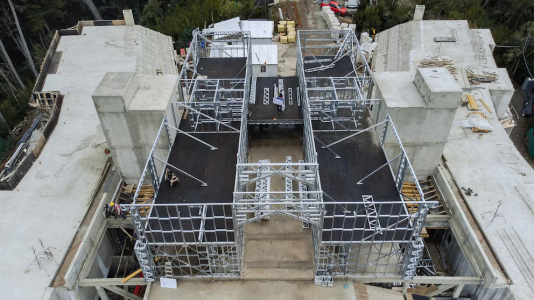
The system can be used to expand or build on pre-existing buildings.
For those considering building or purchasing a property with this system, it is crucial to choose quality materials and hire companies with experience in steel framing.
Steel frame projects are completed in 30% to 50% less time than masonry, thanks to prefabricated pieces
Stange stressed the importance of working with specialized suppliers and builders to ensure the quality and solidity of the constructions. “In addition, I recommend carrying out periodic preventive maintenance to prolong the useful life of the homes,” he added.
Steps to build
The construction process begins with the development of a detailed preliminary project, adapted to the client's needs. This type of project, being industrialized, begins with the manufacturing of parts in the plant, which are then transported for assembly at the site where the house will be built. The modular approach allows for optimizing time and minimizing errors during construction.The work itself consists of several stages: preparation of the ground and foundations, assembly of the steel structure, enclosure with insulating panels and, finally, the interior finishes. This methodology guarantees greater agility in construction, which allows for significantly reduced timeframes compared to traditional methods, while maintaining high quality standards.
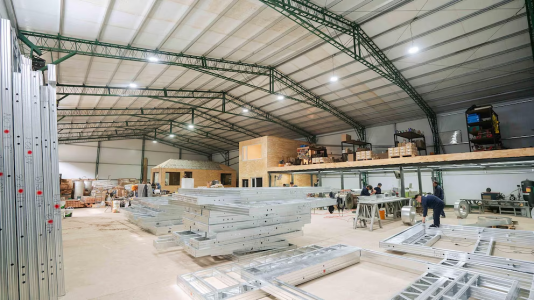
Many of the construction stages are reduced because parts or profiles are built in the factory and then transported to the site or land where they will be built.
Andrés Tilkin , from Sicla and Novafusion, explained that this system is highly versatile and can be adapted to various types of construction. “It is used for single-family homes as well as for hospitals and modular buildings. In addition, it is a viable option both on new land and in remodeling or extensions on pre-existing structures,” he stressed.
In situations where the plan is to build on top of the parents' house, the steel frame is an ideal solution due to its lightness. It allows for adding a floor without overloading the existing structure, provided that the original house is made of reinforced concrete.
When the base structure is also made of steel frame, reinforcements must have been provided from the initial design to support an additional level.
However, when the base structure is also made of steel frame, reinforcements must have been provided from the initial design to support an additional level.
“If the pre-existing steel frame structure was not designed for this additional load, the expansion would not be possible,” explained Aníbal Piczman , from Pirz Construcciones, highlighting the importance of proper structural planning for future expansions.
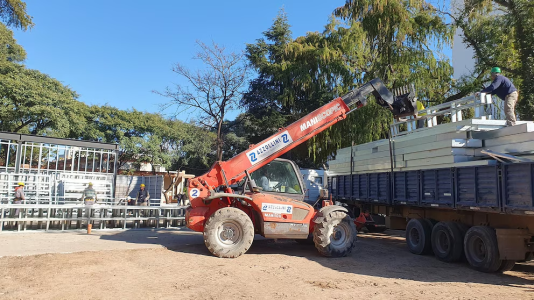
The assembly is fast and not only for homes, it also applies to other constructions.
Flexibility to adapt to different terrains
Steel frame does not necessarily require flat or empty land for its implementation. Andrés Tilkin explained that this system can be applied on sloping land by using concrete slabs or raised bases, which expands the construction possibilities in areas with topographical challenges.“Because it is a lightweight system, it is ideal for adding floors to existing structures, something that is not always feasible with traditional methods,” he said.
Being a lightweight system, it is ideal for adding floors to existing structures, something that is not always feasible with traditional methods (Tilkin)
The type of foundation to be used will depend on the soil analysis and the loads that the structure will have to support.
Aníbal Piczman added that “the most common systems are reinforced concrete slabs, although in some cases punctual bases are used when the ground conditions allow it. This flexibility in the foundations allows the steel frame to adapt to different structural needs, optimizing costs and execution times.”
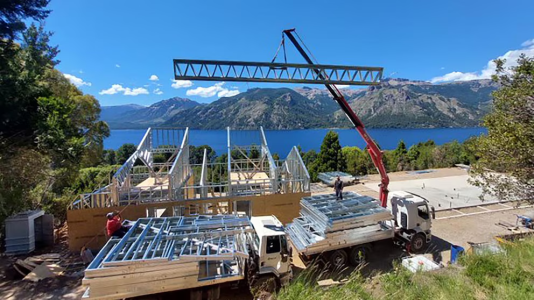
House under construction near San Martin de los Andes
The choice of foundation type depends on the weight of the structure and the quality of the soil, which allows for optimizing the use of materials and reducing costs.
Lifting of the structure and walls
Once the foundation is complete, the structure is assembled. The steel frame pieces are firmly anchored to the base to ensure stability, improving precision and minimising errors during construction.
“Then, it is reinforced with OSB boards - standard oriented strand board made of wood or phenolic, according to the criteria of the construction manager or the engineer in charge,” explained Aníbal Piczman.
“It is essential that the structure is progressively stiffened to prevent movements, rotations or shifting of the steel profiles,” he added, stressing the importance of stability at this stage.
Insulation and coatings
After the structure is installed, thermal and acoustic insulation materials are incorporated, which not only improve interior comfort, but also contribute to the energy efficiency of the building.
These insulators are essential to ensure that the home is efficient in terms of energy consumption, which translates into lower heating and cooling costs in both winter and summer.
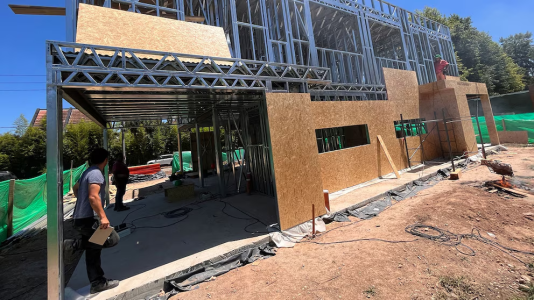
In the private neighborhoods there are hundreds of houses in action. Here you can see how they are closed with panels made of wood.
Tilkin explained that OSB panels are used for the enclosures along with wind and water barriers, ensuring the protection of the structure. “The exterior finish can include cement, wood or siding cladding, depending on the desired design,” he said.
After installing the pipes in walls and floors, comprehensive insulation is carried out, covering ceilings and floors.
“It is common to use sprayed cellulose, an ecological material with excellent thermal and acoustic insulation properties, which also resists exposure to fire without spreading flames or emitting smoke,” explained Tilkin.
Interior coverings
Once this process is complete, interior coverings are applied, which may include plasterboard, textured paints, wood, stone finishes or veneers, according to the owner's preferences.Aníbal Piczman estimated that a 70-square-meter home can be completed in a period of between four and six months. “This translates into significant savings in labor costs and indirect expenses, which is especially advantageous in inflationary contexts,” he said.
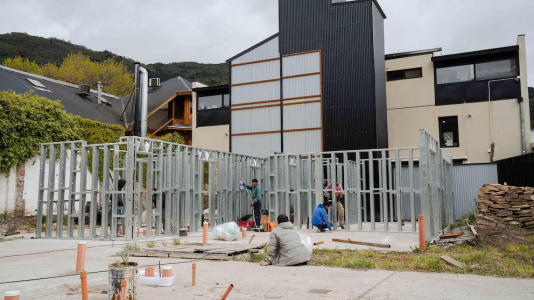
The house is built in less than a year
From the beginning of the work to its completion, up to 12 workers can be involved. In addition, these homes are evolutive, which means that they can be expanded in rooms and spaces using the same steel profiles.
Some of the benefits
Among the less obvious benefits of steel framing are the reduction in freight and dump truck costs. Piczman explained: “The clean-up and organization of the construction site are much more efficient, which reduces costs for expenses, construction fees and other operating expenses.”Currently, a standard home is built at a rate of USD 1,100 per m2 and something more premium starts at USD 1,400, everything depends on the available budget and there is bank financing through the new mortgage loans , which facilitates access to this type of construction.
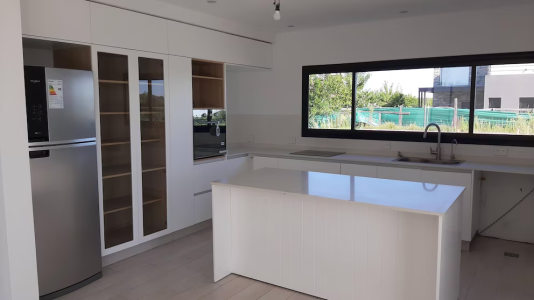
The rooms are finished with the same materials used in the traditional format.
As for the finishes, there are various options that impact the final cost. “Using Modena line openings with 3x3 laminated glass is not the same as opting for a superior quality, such as the A30 system with double hermetic glass (DVH),” explained the sector.
Variability is also observed in floors and coverings, where the price range is wide, as well as in fixtures and taps, which can be adjusted to different budgets according to the owner's preferences.
Staff and training
Success in steel frame construction depends on having a trained workforce.According to Andrés Tilkin, a team of approximately five people is required for a 70 m² dwelling. Technical training and experience in this method are essential to ensure the quality and efficiency of the project, resulting in faster and more accurate execution.
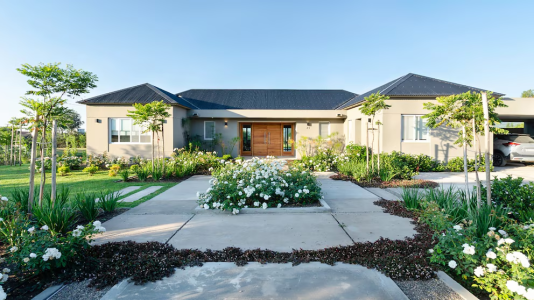
Ready to move in housing
However, Aníbal Piczman stressed that finding experienced steel frame workers remains a challenge in the local market.
“Labor represents approximately 30% of the total cost of the work, so it is essential to have specialized personnel,” he emphasized. Lack of adequate training can delay execution times and affect the quality of the project.
Scalability and future expansion
One of the great advantages of the steel frame is its ability to expand. Being a modular system, it allows for the addition of new levels or rooms, as long as this possibility is contemplated in the initial design. This makes it an ideal option for those planning to expand their home in the long term, adapting to the changing needs of families."This system represents the future of construction in a context where inflation and rising material prices are impacting the traditional sector," concluded Piczman.
www.buysellba.com