BuySellBA
Administrator
Premises, offices, houses and buildings: modular construction drives new businesses due to its ease of assembly and disassembly - La Nacion Propiedades
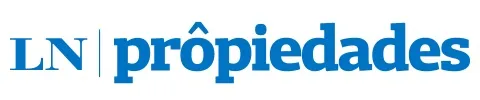
Source:
www.lanacion.com.ar
July 14, 2024
In Argentina, demand is concentrated in industry and commerce with premises and offices above houses; there are few large factories in the country.
By Gabriela Origlia
Even in traditionally constructed buildings, modular parts can be included.
CORDOBA.- Modular construction is gaining ground in Argentina. The evolution of the system allows for a flexibility that was unthinkable for the traditional system. For now, there are very few large companies, but there has been an increase in the number of SMEs that collaborate to expand and spread general knowledge about factory construction , with parameters that are similar to those followed by the automotive industry. Industrial and commercial demands are still the most important, above residential demands. The needs of oil and mining companies to develop camps in the regions where they operate play a key role .
The advantages of the system are speed - a job that can take a year using the traditional method now takes three or four months - sustainability (less waste, energy savings ) and the possibility of moving the structures to inhospitable areas, either due to geography or climate, where it is much more difficult to have people working or to move materials. The parts or the complete unit are moved by truck to the place where they are to be installed.
Modular buildings are created in factories and transported
Costs, in some cases, can be between 10% and 20% higher than the traditional system, basically due to the impact of logistics to move the construction. However, specialists say that, if breakages, thefts and construction time are taken into account, the “ total amount is compensated.”
The Unimod company, part of the Azzollini Construcciones group, is a pioneer in modular construction in the country (it started 30 years ago). For example, it built the YPF camp in Vaca Muerta. It operates in Argentina and also exports to neighboring countries from its factory in Buenos Aires . They build modular buildings .
Another important player is the Cordoba-based developer Edisur, which launched Caps in 2017, through its area specialising in dry construction using the SteelFrame system. The business unit was created with the concept of a “capsule” in mind to offer a “quality, technological and efficient” housing solution , both in terms of energy and logistics.
Federico Azzollini, managing partner of Azzollini Construcciones, explains that since they started, they have been constantly improving their processes, which has allowed them to have a “ building manufacturing plant in a controlled environment, with structures that are transported in parts to the final destination . We have optimized the processes, which has allowed us to lower costs and guarantee deadlines , a key aspect.”
The company is now working with the concept of “ evolutionary building solutions ” which means that units can be reduced or enlarged over time: “It is disruptive and has a great impact. The buildings are assembled in a weekend with the consequent reduction in waste and carbon footprint.” He says that there are developers who are beginning to turn to this system which allows them, for example, to move forward with parts of buildings that are inside traditional structures; they market modular solution kits (for example, a bathroom and laundry room) and the rest in panels, so that “the house is assembled dry without the need for it to be complete, and then more can be added .”
From Edisur, Horacio Parga (h) states that, at first, they built houses for places that were difficult to reach, but they were “ evolving to seek volume production” . Last year they built 2000 meters per month between houses, shops, factory facilities and classrooms for the Province of Córdoba. “There were 75 that allowed them to be installed where they were needed, in a short time - he specifies -. In the case of a mall, it can be set up and then change areas . These are very interesting facilities”.
Argentina's largest company, Unimod, manufactures luxury homes and transports them to Uruguay.
Azzollini agrees that the modular construction system “ opens up new business segments; a landowner could lease it for example” due to the flexibility of installing the required unit and then being able to relocate it and take it to another space. The company has a system of rental offices at home. “ There are various alternatives that can be worked with - he says -. We make luxury houses for Uruguay at an Argentine cost , much lower than what they cost there, and then we take them and install them.”
The system allows for the construction of shopping centres that can later be replaced by traditionally constructed ones, or removed.
Beyond the demand of industry and commerce, in the last two years in Argentina the modular system has been used a lot for tourism projects. Experts emphasize that, for any type of work -depending on the scale- it is necessary to be technically qualified . “Not everyone can do any work, it requires years and continuous training processes,” summarizes Azzollini.
www.buysellba.com
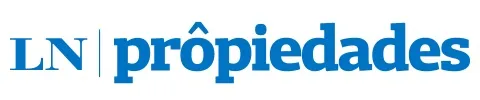
Source:

Locales, oficinas, casas y edificios: la construcción modular impulsa nuevos negocios por su facilidad para montar y desmontar
En la Argentina la demanda se concentra en la industria y el comercio con locales, oficinas por encima de las casas; hay pocas fábricas grandes en el país

July 14, 2024
In Argentina, demand is concentrated in industry and commerce with premises and offices above houses; there are few large factories in the country.
By Gabriela Origlia

Even in traditionally constructed buildings, modular parts can be included.
CORDOBA.- Modular construction is gaining ground in Argentina. The evolution of the system allows for a flexibility that was unthinkable for the traditional system. For now, there are very few large companies, but there has been an increase in the number of SMEs that collaborate to expand and spread general knowledge about factory construction , with parameters that are similar to those followed by the automotive industry. Industrial and commercial demands are still the most important, above residential demands. The needs of oil and mining companies to develop camps in the regions where they operate play a key role .
The advantages of the system are speed - a job that can take a year using the traditional method now takes three or four months - sustainability (less waste, energy savings ) and the possibility of moving the structures to inhospitable areas, either due to geography or climate, where it is much more difficult to have people working or to move materials. The parts or the complete unit are moved by truck to the place where they are to be installed.
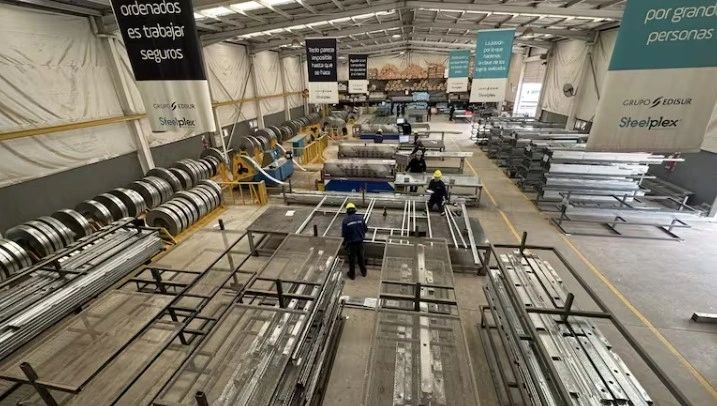
Modular buildings are created in factories and transported
Costs, in some cases, can be between 10% and 20% higher than the traditional system, basically due to the impact of logistics to move the construction. However, specialists say that, if breakages, thefts and construction time are taken into account, the “ total amount is compensated.”
The Unimod company, part of the Azzollini Construcciones group, is a pioneer in modular construction in the country (it started 30 years ago). For example, it built the YPF camp in Vaca Muerta. It operates in Argentina and also exports to neighboring countries from its factory in Buenos Aires . They build modular buildings .
Another important player is the Cordoba-based developer Edisur, which launched Caps in 2017, through its area specialising in dry construction using the SteelFrame system. The business unit was created with the concept of a “capsule” in mind to offer a “quality, technological and efficient” housing solution , both in terms of energy and logistics.
Federico Azzollini, managing partner of Azzollini Construcciones, explains that since they started, they have been constantly improving their processes, which has allowed them to have a “ building manufacturing plant in a controlled environment, with structures that are transported in parts to the final destination . We have optimized the processes, which has allowed us to lower costs and guarantee deadlines , a key aspect.”
The company is now working with the concept of “ evolutionary building solutions ” which means that units can be reduced or enlarged over time: “It is disruptive and has a great impact. The buildings are assembled in a weekend with the consequent reduction in waste and carbon footprint.” He says that there are developers who are beginning to turn to this system which allows them, for example, to move forward with parts of buildings that are inside traditional structures; they market modular solution kits (for example, a bathroom and laundry room) and the rest in panels, so that “the house is assembled dry without the need for it to be complete, and then more can be added .”
From Edisur, Horacio Parga (h) states that, at first, they built houses for places that were difficult to reach, but they were “ evolving to seek volume production” . Last year they built 2000 meters per month between houses, shops, factory facilities and classrooms for the Province of Córdoba. “There were 75 that allowed them to be installed where they were needed, in a short time - he specifies -. In the case of a mall, it can be set up and then change areas . These are very interesting facilities”.
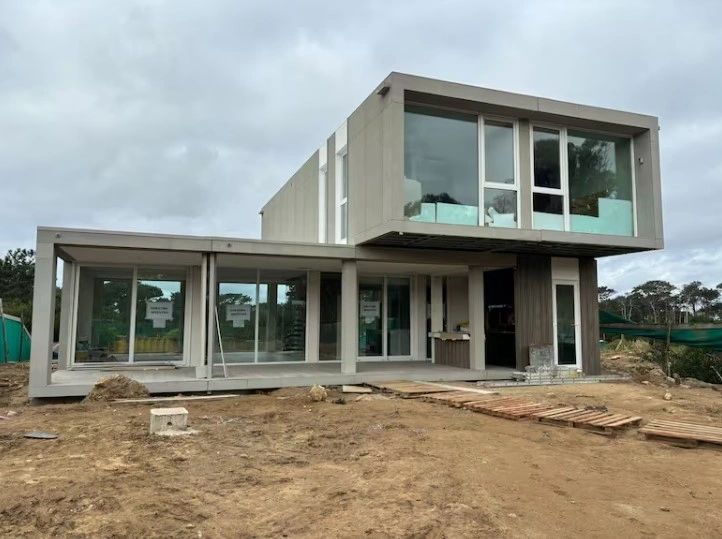
Argentina's largest company, Unimod, manufactures luxury homes and transports them to Uruguay.
Changes in the business
For the company, it is also a “ complement” to the real estate land business that it carries out as a developer. “Whoever buys a lot can have a 100 or 150 square meter house with all the comforts in 90 days. We are also analyzing several projects in mining areas of Salta, Catamarca and San Juan and in oil destinations ,” he says.Azzollini agrees that the modular construction system “ opens up new business segments; a landowner could lease it for example” due to the flexibility of installing the required unit and then being able to relocate it and take it to another space. The company has a system of rental offices at home. “ There are various alternatives that can be worked with - he says -. We make luxury houses for Uruguay at an Argentine cost , much lower than what they cost there, and then we take them and install them.”
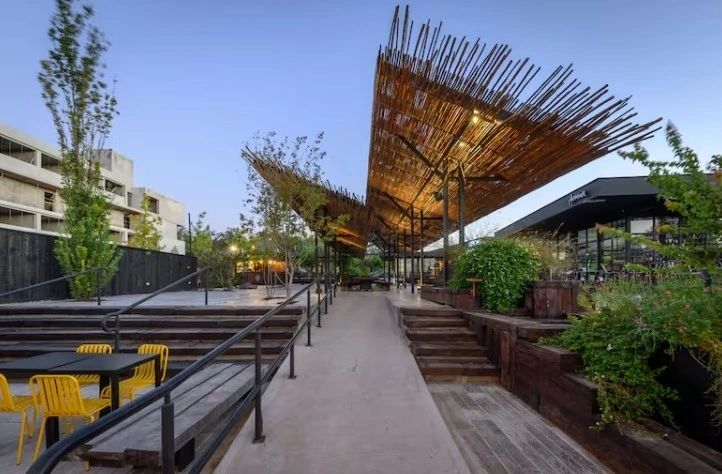
The system allows for the construction of shopping centres that can later be replaced by traditionally constructed ones, or removed.
Beyond the demand of industry and commerce, in the last two years in Argentina the modular system has been used a lot for tourism projects. Experts emphasize that, for any type of work -depending on the scale- it is necessary to be technically qualified . “Not everyone can do any work, it requires years and continuous training processes,” summarizes Azzollini.
www.buysellba.com