BuySellBA
Administrator
Steel and industrialized construction allow savings of up to 60% in construction times: costs of a booming system - Infobae
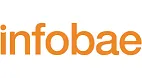
Source:
www.infobae.com
October 03, 2024
More than 10,000 units of this type are built in the AMBA. The housing parts are transported and assembled on site. Assembly does not depend on weather conditions.
By Jose Luis Cieri
Industrialized construction optimizes costs, reduces waste and shortens execution times (Illustrative Image Infobae)
The industrialized construction system is revolutionizing the way homes and buildings are built. The modules that make up structures such as walls and roofs are produced in factories, under strict international standards, optimizing resources and reducing waste, compared to traditional systems that use sand, lime and cement on the construction site.
Currently, there are an estimated 10,000 units under construction between the city of Buenos Aires and Greater Buenos Aires (GBA), driven mainly by families moving to private or semi-open neighborhoods in the suburbs. There is also a growth in buildings being built in Buenos Aires neighborhoods such as Boedo, Villa Crespo, Palermo, Chacarita and Monte Castro, among others.
Using this material in this type of construction has clear benefits, as highlighted in the industry. Carlos Vaccaro , executive director of the Argentine Chamber of Steel, said that its versatility, resistance and 100% recyclability make it ideal for sustainable projects. “In addition, the use of high-density steel has been shown to reduce carbon emissions by 20% to 30%, thanks to the fact that it allows for building with lighter and more efficient structures,” he said.
The traditional image of a construction site is changing. Today, those who already have land or air space on an existing building prefer to avoid the traditional process of erecting walls brick by brick with sand, lime and cement. Instead, the walls arrive directly from the plant, produced in a controlled environment, ready to be assembled on site.
The advantages of industrialized systems are reflected in several aspects, including the optimization of construction deadlines.
Vaccaro highlighted the standardisation of products, the precision between design and execution, energy efficiency and less dependence on climate during assembly. “Module production not only minimises labour risks but also considerably reduces construction times, reaching up to 60% less than in traditional works,” he added.
Another common technique is the use of pre-reinforced concrete, where much of the production is done in-house. There are also options with independent metal structures and Steel Deck slab systems.
Industrialized construction offers advantages in maintenance and energy efficiency.
The incorporation of thermal and acoustic insulation in the panels improves the efficiency of buildings, achieving significant savings of up to 20% on bills.
Vaccaro stressed the importance of having the right personnel to carry out these projects. “The logistics and transport of large modular components require detailed planning and rigorous quality control to ensure that all elements fit together correctly, thus meeting the design objectives,” he said.
Furthermore, since the modules are produced in a controlled environment such as a factory, the occupational risk is reduced (Illustrative Image Infobae)
Modular construction is not limited to private homes, but is suitable for a variety of buildings.
A 100 square meter house can be built by 6 people in a period of 100 to 120 days.
Another important advantage is the optimisation of the project. For example, to realise the dream of owning a home, the factories produce complete modules according to the client's choice. In most cases, no mortar or mix is required. This also means that their assembly does not depend on climatic conditions, as is the case with traditional systems.
House made of steel and with a modern European country design
“As for the current values per m2 of units built in steel, the reality is that it varies according to models and finishes, with a range that goes, approximately, between USD 900 and USD 1,300,” said Fernando Perroni , an architect specialized in dry construction.
And a house finished with this material with 100 m2 and three bedrooms in private neighborhoods costs from USD 135,000 and up.
Buildings are also built where the steel structure is crucial to the work.
In Buenos Aires there are apartments currently under construction with prices ranging from USD 100,000 for one-bedroom apartments and USD 135,000 for brand new two-bedroom apartments.
The system is not only applicable to residential homes, but is also ideal for the construction of housing complexes such as university residences. Currently, in Añelo, near Vaca Muerta, more than 1,000 homes are being built to meet the rental demand of those who move to the area to work in the hydrocarbon basin located in the province of Neuquén.
The greater lightness of masonry, which makes it possible to support the load with less structure, is also an advantage to consider.
“Linked to this, a lower requirement for columns and walls expands the interior spaces and their functional and decorative possibilities,” Vaccaro concluded.
www.buysellba.com
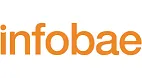
Source:

El acero y la construcción industrializada permiten ahorrar hasta un 60% en los plazos de obra: costos de un sistema en auge
Se construyen más de 10.000 unidades de este tipo en el AMBA. Las partes de la vivienda se transportan y ensamblan en el lugar. El montaje no depende de las condiciones climáticas

October 03, 2024
More than 10,000 units of this type are built in the AMBA. The housing parts are transported and assembled on site. Assembly does not depend on weather conditions.
By Jose Luis Cieri
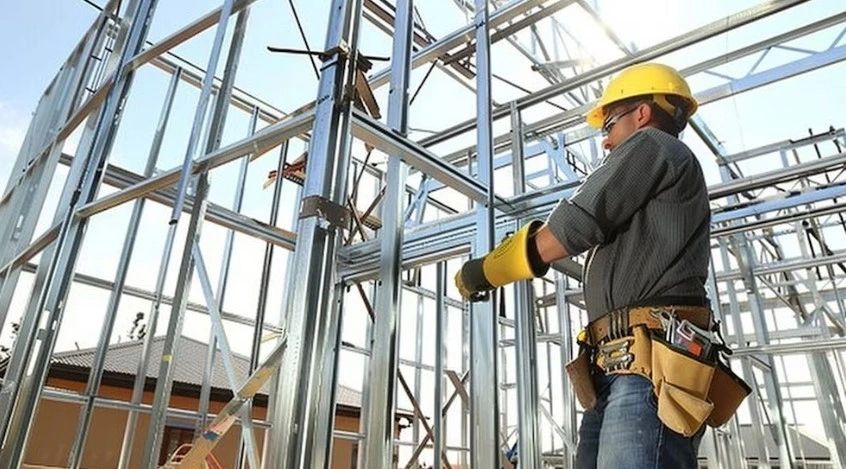
Industrialized construction optimizes costs, reduces waste and shortens execution times (Illustrative Image Infobae)
The industrialized construction system is revolutionizing the way homes and buildings are built. The modules that make up structures such as walls and roofs are produced in factories, under strict international standards, optimizing resources and reducing waste, compared to traditional systems that use sand, lime and cement on the construction site.
Currently, there are an estimated 10,000 units under construction between the city of Buenos Aires and Greater Buenos Aires (GBA), driven mainly by families moving to private or semi-open neighborhoods in the suburbs. There is also a growth in buildings being built in Buenos Aires neighborhoods such as Boedo, Villa Crespo, Palermo, Chacarita and Monte Castro, among others.
Using this material in this type of construction has clear benefits, as highlighted in the industry. Carlos Vaccaro , executive director of the Argentine Chamber of Steel, said that its versatility, resistance and 100% recyclability make it ideal for sustainable projects. “In addition, the use of high-density steel has been shown to reduce carbon emissions by 20% to 30%, thanks to the fact that it allows for building with lighter and more efficient structures,” he said.
The traditional image of a construction site is changing. Today, those who already have land or air space on an existing building prefer to avoid the traditional process of erecting walls brick by brick with sand, lime and cement. Instead, the walls arrive directly from the plant, produced in a controlled environment, ready to be assembled on site.
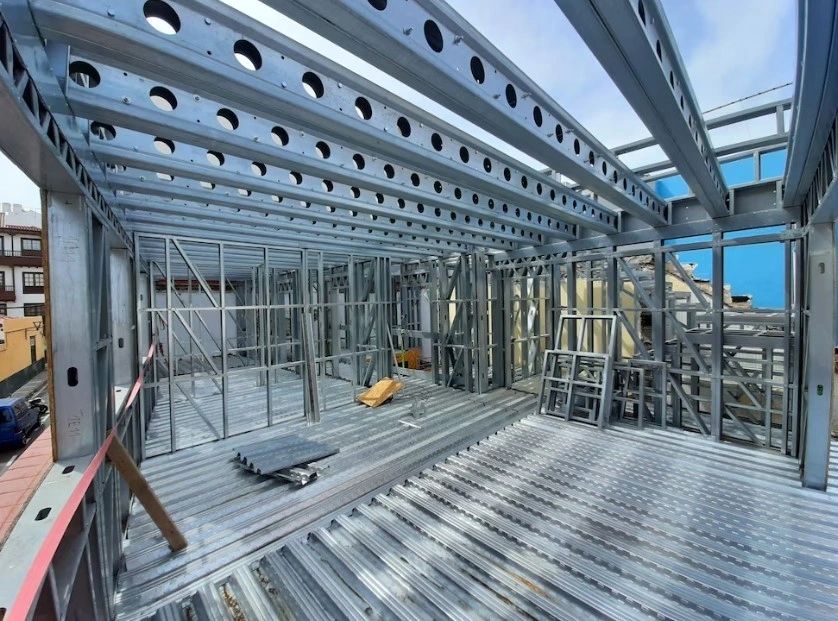
The advantages of industrialized systems are reflected in several aspects, including the optimization of construction deadlines.
Vaccaro highlighted the standardisation of products, the precision between design and execution, energy efficiency and less dependence on climate during assembly. “Module production not only minimises labour risks but also considerably reduces construction times, reaching up to 60% less than in traditional works,” he added.
Galvanized
Lightweight construction, based on galvanized steel profiles, is the most common and is known as steel framing . This methodology allows for the construction of structures of up to three floors and is ideal for different types of buildings, from homes to classrooms and industrial warehouses.Another common technique is the use of pre-reinforced concrete, where much of the production is done in-house. There are also options with independent metal structures and Steel Deck slab systems.
Industrialized construction offers advantages in maintenance and energy efficiency.
Prefabricated steel materials ensure durability and precision, reducing future repairs
The incorporation of thermal and acoustic insulation in the panels improves the efficiency of buildings, achieving significant savings of up to 20% on bills.
Vaccaro stressed the importance of having the right personnel to carry out these projects. “The logistics and transport of large modular components require detailed planning and rigorous quality control to ensure that all elements fit together correctly, thus meeting the design objectives,” he said.
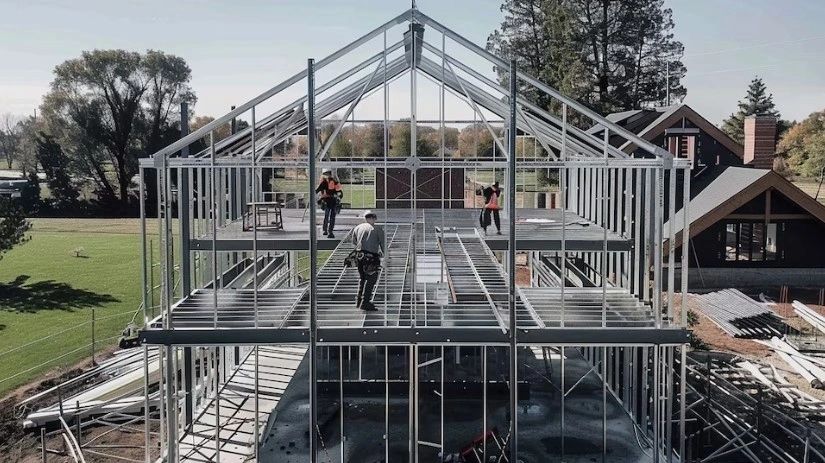
Furthermore, since the modules are produced in a controlled environment such as a factory, the occupational risk is reduced (Illustrative Image Infobae)
Modular construction is not limited to private homes, but is suitable for a variety of buildings.
A 100 square meter house can be built by 6 people in a period of 100 to 120 days.
Another important advantage is the optimisation of the project. For example, to realise the dream of owning a home, the factories produce complete modules according to the client's choice. In most cases, no mortar or mix is required. This also means that their assembly does not depend on climatic conditions, as is the case with traditional systems.
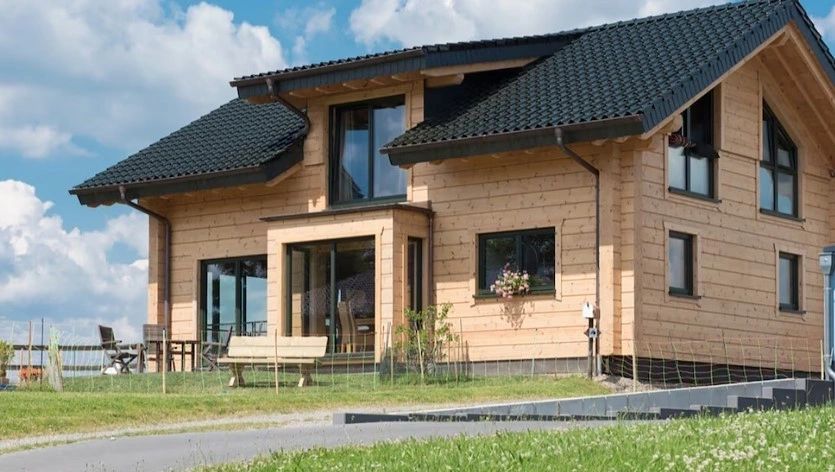
House made of steel and with a modern European country design
Numbers
Costs have generally followed inflation in recent years, with a significant difference in the first quarter of this year, when inflation was assumed to be much higher than it ultimately was, and therefore prices had to be adjusted downwards recently due to the drop in the inflation rate.“As for the current values per m2 of units built in steel, the reality is that it varies according to models and finishes, with a range that goes, approximately, between USD 900 and USD 1,300,” said Fernando Perroni , an architect specialized in dry construction.
And a house finished with this material with 100 m2 and three bedrooms in private neighborhoods costs from USD 135,000 and up.
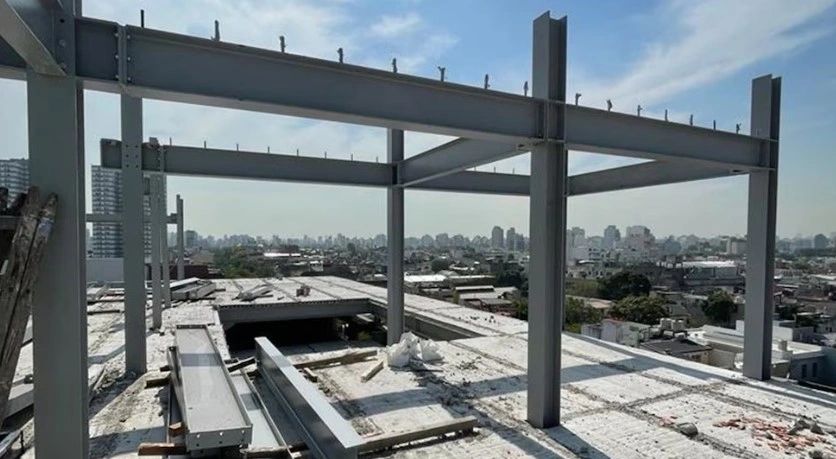
Buildings are also built where the steel structure is crucial to the work.
In Buenos Aires there are apartments currently under construction with prices ranging from USD 100,000 for one-bedroom apartments and USD 135,000 for brand new two-bedroom apartments.
The system is not only applicable to residential homes, but is also ideal for the construction of housing complexes such as university residences. Currently, in Añelo, near Vaca Muerta, more than 1,000 homes are being built to meet the rental demand of those who move to the area to work in the hydrocarbon basin located in the province of Neuquén.
The greater lightness of masonry, which makes it possible to support the load with less structure, is also an advantage to consider.
“Linked to this, a lower requirement for columns and walls expands the interior spaces and their functional and decorative possibilities,” Vaccaro concluded.
www.buysellba.com