BuySellBA
Administrator
The houses that should be built in a context with inflation - La Nacion Propiedades
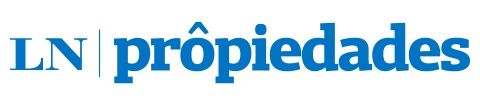
Source:

Las casas que conviene construir en un contexto con inflación
Las casas modulares se presentan como una buena oportunidad de inversión, frente al contexto de inflación y aumento del costo de construcción

March 12, 2024
Modular houses are presented as a good investment opportunity, in the context of inflation and increased construction costs.
By Maria Josefina Lanzi
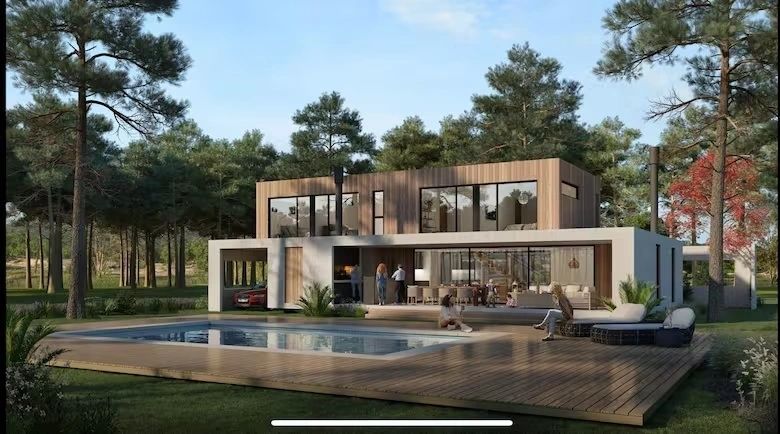
Modular homes are constructions with many advantages and can beat inflation
The excitement of starting a new house often disappears when the first obstacles and delays in construction arise . Although the dream of building a housing project is great, it is common knowledge that the works take and always take longer than planned , directly impacting the initial costs that had been raised.
Faced with this context, the inflation that the country is experiencing and the increase in the cost of construction, there is an option that has been emerging for some time, which can be carried out in a period of less than six months and, little by little, it is taking more flight: modular houses.
Modular houses are constructions that are made in a factory, in three dimensions, on a production line similar to an automotive industry, with different processes that range from the manufacturing and assembly of the metal structure to the final finishes. Once completed, they are transported in parts, in trucks with carts, to the land where they will be located . Each module arrives at its destination with the floor, walls, ceiling, windows and doors made and installed.
There is a wide variety of options, models and prices within the universe of modular houses, but many of their advantages are shared: they provide a more controlled quality , since they are manufactured in a plant, which allows a precision of 2mm; They have a faster execution speed , use a more sustainable process with less environmental impact and can be made with materials that can be recycled almost entirely. “In this economy that is reflected in a cost advantage. If they deliver it to you in four months, instead of 24, there is a very important difference in value due to inflation ,” says Lucas Salvatore, president of Idero.
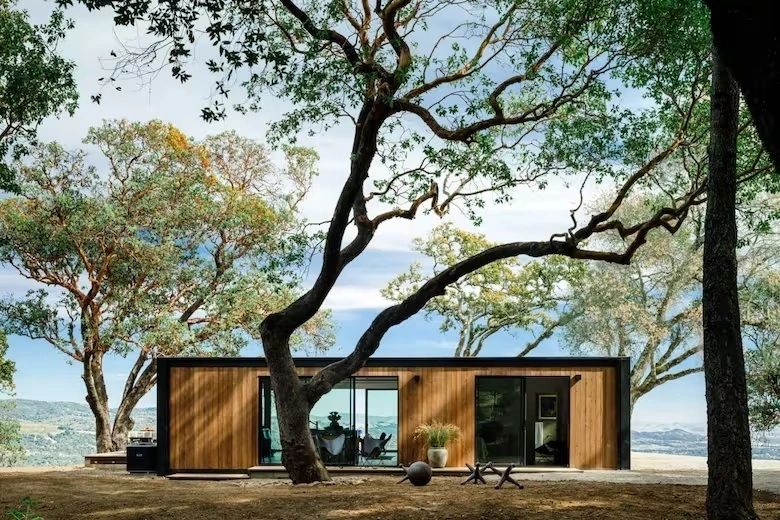
Modular houses have faster execution speed, a more sustainable process and less environmental impact
In addition, by being built in a factory, the need to go to the construction site if it is far away or deal with possible conflicts from a distance is avoided. “Today we are making premium houses for Punta del Este, Patagonia or the north of the country , but we are building them in our workshop in Ezeiza,” says architect Federico Azzollini, managing partner of Grupo Azzo, where they work making modular houses from more than 30 years ago.
Marta Oriozabala, a real estate lawyer and founder of Evolutiva , assures that lately they have had a greater number of queries and see greater confidence in the system and technology. The president of the Business Chamber of Urban Developers (CEDU), Damián Tabakman, believes that, although it is not easy to convince someone to adopt this technology, “they have many advantages and a great future . ”
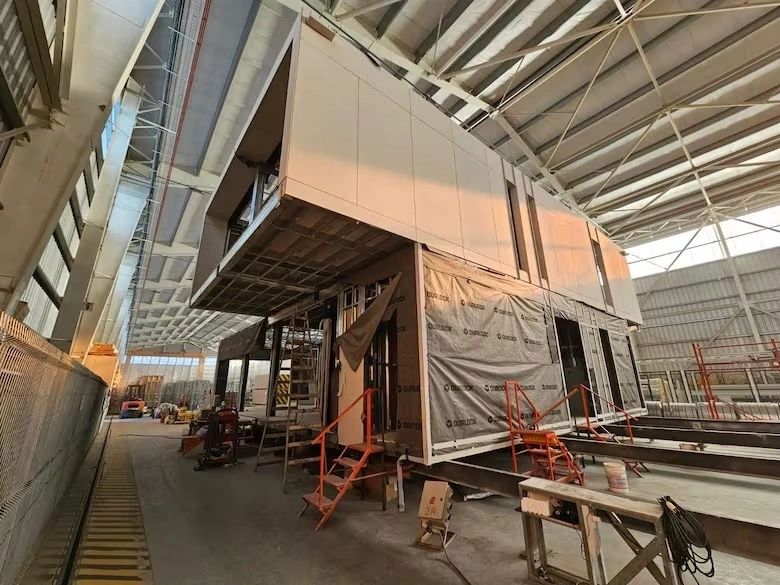
By being built in a factory, one avoids going to the construction site if it is far away or dealing with unions from a distance.
Record times for the world of construction
One of the main characteristics of modular houses is that the execution time is shorter than that of traditional construction because it is done between four to six months . This is achieved because it is possible to work within a factory with the materials at hand, avoiding inclement weather (such as rain), which alters the work process. In addition, it allows tasks to be overlapped, since while the excavation and foundations are carried out, the house can be built inside a factory . “This means beating inflation, since there is a quick recovery of the investment,” comments architect Azzollini.In this sense, regarding the acceleration of times, Azzolini details that "it is possible to reduce up to half of what a traditional construction takes." And he explains that everything depends on the type of architecture you decide to make, how complex the finishes are. In their case, Grupo Azzo offers products with a value similar to that of traditional construction, which vary depending on the location, land where the house will be located and the quality with which it will be built.
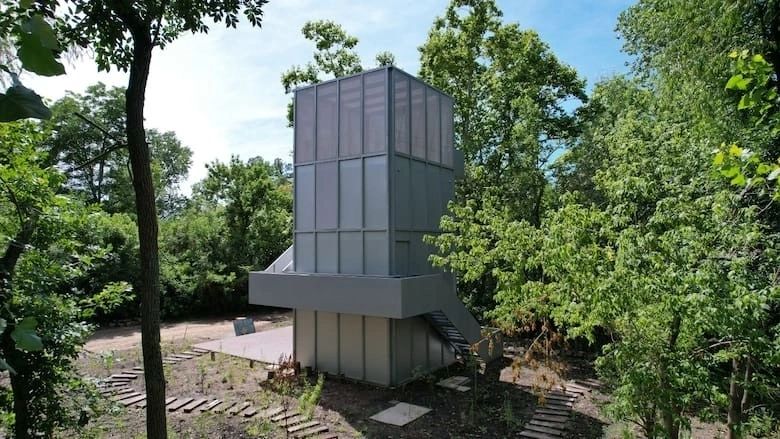
Approximately 80% of the house is built in the factory and then moved to the destination land
Unlike traditional construction systems, which are more artisanal, modular houses, as they are produced within a factory and have industrialized structures and enclosures, such as the steel frame construction system , there is also the advantage of ensuring that the design of the envelope (ceilings, floors and exterior walls), arises from the measurement of its components according to the performance of the materials that compose it and results as calculated.
Salvatore shares that, in addition to reducing construction deadlines, much more precision in costs and duration is achieved. “In a country where certainty is not abundant, a little security does not hurt ,” he points out and adds that the structure is manufactured in the plant with a precision of 2mm.
Prices and models
In Idero, they have houses ranging from 150 m² to 500 m² that are around US$1600/m². They also offer smaller options, of 48 m² and 60 m², which today are around US$58,000 and US$72,000 , respectively, with the revaluation of the peso.In the world of traditional construction, more than half of the houses are built for an estimated price at the beginning and then it is adjusted over the course of the work as materials are purchased, salaries, supplies, taxes are paid. , among other expenses.
In this regard, architect Octavio Roca, from the CAS4 team, says: "Whoever makes industrialized or modular houses can give you the price of the house before you decide whether to buy it or not." For its part, the value per m² in CAS4 is around US$ 1,500 , although it varies according to the levels and quality of finishes and size (they have models ranging from 24 m² to 120 m² ). In the case of Evolutiva they offer houses with an approximate price of US$1200/m² .
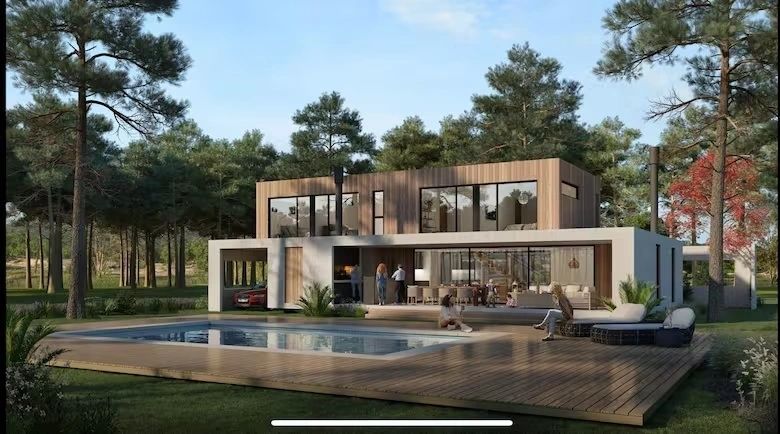
In Punta del Este, houses are being built with this construction technique
In his case, he says that the construction time ranges from three to six months, depending on the demand they have : “Approximately 80% of the house is built in the factory and then it is moved to the destination land.”
Sustainability has its economic benefits
The issue of costs is a question that arises when analyzing this construction model. Some experts point out that it is difficult to generalize whether they are more expensive or not than traditional houses, since there are many variables that must be considered and that change depending on how they are built (the type of finishes or the insulation used). Roca says that, in his case, the modular constructions they make require a significant initial investment, but points out that “ an efficient house costs a little more up front, but not so much later, because it is not that expensive to maintain .” He explains that a house is evaluated not only by its initial price, but by how long it will last and the expenses it will involve over time. “These houses are super efficient and when you compare the cost of use and maintenance of each one, the economy over the years is 5 to 1: that is, the bill for the cost of services is five times lower than that of a common house,” adds the architect.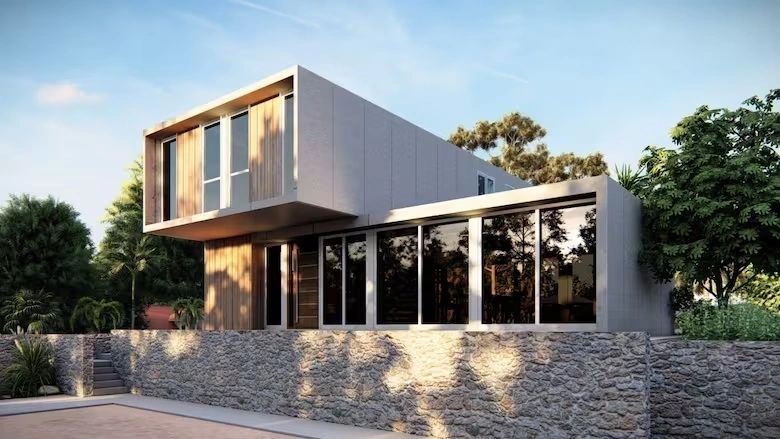
Modular houses are very efficient in use and maintenance
Federico Azzolini explains that modular houses can be designed depending on the bioclimatic zone where they will be located . In this way, thermal insulation calculations are made, based on the temperatures that will surround them: “This translates into being energy efficient : savings on supplies, such as electricity and gas.”
Furthermore, since it is produced in a factory and then taken to the field, the impact on the environment is much lower . Azzolini adds that “it is typical of the work model, at least ours, to reduce the waste of materials. We manufacture with a panelized structural steel frame system , which is custom-made, with prior modeling and under a structural calculation, which leads to avoiding waste.”
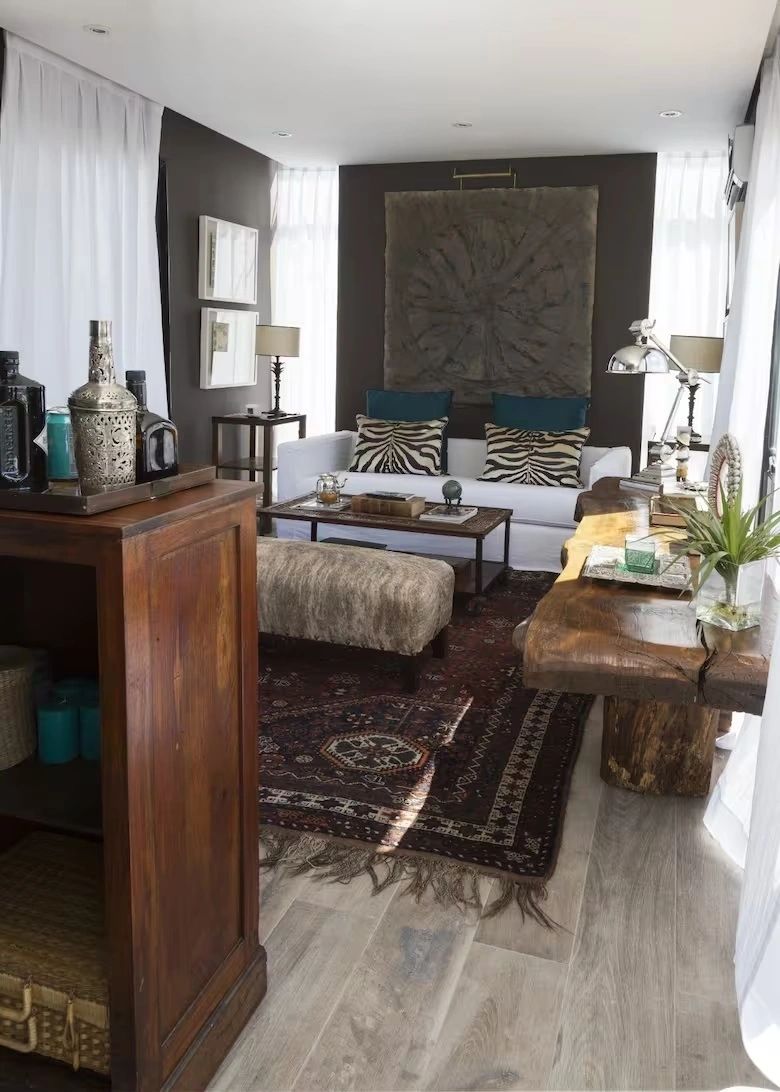
In modular homes you can start with a two-bedroom module, and then add more or even build upwards.
A transportable house
Another element that adds added value to these constructions, applicable to both houses and buildings, is that they can be moved from one place to another. This provides an advantage for those places where getting construction material or labor is difficult, and for those destination areas where the presence of a house is no longer required.30 years ago, the Azzo group began to venture into modular homes, following a request made by an oil company with which they worked. They needed comfortable homes suitable for hostile areas with high temperature ranges, strong winds and other inclement weather , where workers who worked in oil companies lived. The result was that they managed to generate modular constructions “with a premium demand.”
Lucas Salvattore explains that: “If within three years Vaca Muerta does not have the potential it has today, there is the possibility of relocating the constructions that were made and taking them to Jujuy, if necessary.” Currently, his team is constructing a total of 17 modular buildings in the area (divided into three stages). With a steel structure, it will generate a lower carbon footprint, will be fully recyclable and will be built with great precision.
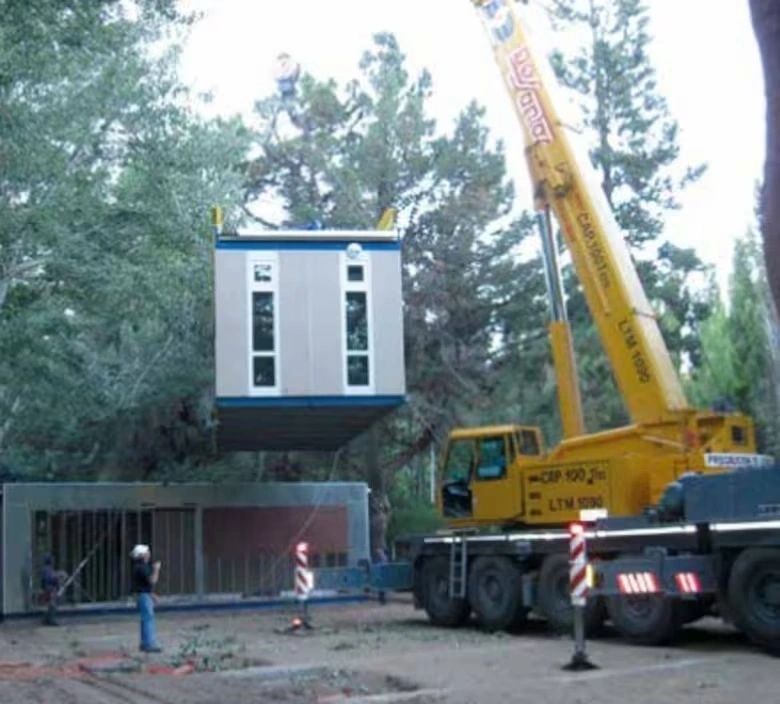
A great advantage of modular homes is that they can be transported, allowing construction materials or labor to be delivered to hard-to-reach places.
Another great virtue is that modular houses that have the steel frame construction system in their structure have less thickness in the envelope (exterior walls, ceilings and floors) . That equates to more useful surface area, whether larger rooms or more of them. Furthermore, they are made with an evolutionary architecture system , that is, one can start by building a small first space, but with the aspiration that, as economically possible, the house is enlarged by blocks.
In that sense, Marta Oriozabala, from Evolutiva, explains: “You can start with a 42 m² two-room module and then add more or even build upwards. In addition, the walls are much thinner, with a thickness of only 15 cm, which means that the house is lighter and offers more space within the available square meters .”
www.buysellba.com