BuySellBA
Administrator
What is the first precast concrete residential condominium in the country like? - La Nacion Propiedades
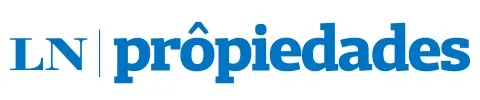
Source:
www.lanacion.com.ar
October 08, 2024
The plates are a development of a local construction group in the province of Córdoba; the system reduces execution times by up to 70% and the associated costs are more predictable.
By Gabriela Origlia
The project in Córdoba will have 10,000 square meters on a 14,000 m2 plot.
CORDOBA.- A real estate development built with precast concrete inaugurated in the northern area of the city of Córdoba , became the first residential condominium in the country built entirely with this technology that reduces construction times by up to 70% while costs have “greater predictability.”
The Garderie residential development has 78 one- and two-bedroom units , ranging from 90 to 110 m², plus a garage; it was designed by the Córdoba-based developer Meade-Pucheta, while the precast concrete is manufactured by Grupo Astori. The walls, load-bearing elements, stairs, floors, beams and columns are industrialized under processes certified with Iso-Iram standards.
Precast concrete is transported from the factory to the construction site and installed so quickly that it significantly reduces the time compared to traditional methods . “The development of this system required us to go beyond what was known, to work meticulously on every detail and to offer an innovative product that responds to the demands of efficiency in construction . We believe that it will revolutionize the construction industry in Argentina,” says María Pía Astori , president of Grupo Astori.
The development has amenities such as a swimming pool, two barbecue areas, as well as a surveillance system and security cameras. Martin Dahan , director of Meade-Pucheta, points out that it is an opportunity for both those who want to live there and for investors .
There are apartment walls that maintain the concrete slabs unchanged.
The construction system is a development by the Cordoba group, the result of “exhaustive research” on what exists internationally. They indicated that they studied models in countries with extreme climates, where thermal insulation is essential . These inspired them to design their “sandwich panels, a combination of concrete, expanded polystyrene and a structural mesh .”
The system was adapted to market conditions in Argentina and a methodology was developed that allows for efficient manufacturing in its industrial plants in Córdoba and Buenos Aires, “maintaining a balance between quality, design, and costs, so that the product is highly competitive.”
For each project, the pieces are custom-made to suit the architectural and functional requirements. The construction company explains that the solution is “specifically designed for real estate developments such as housing, buildings, condominiums, collective housing and similar projects.”
In the case of the project in Córdoba, a tower was completed in eight months: the structural part took 60 days and the rest of the work 180 days. This time is equivalent to assembling an entire apartment in just three days. The largest panel used on the façade is a single piece measuring 12 metres high by three metres wide, spanning three floors; it is placed in a single movement, structuring the building and, at the same time, assembling the bedroom closets.
Concrete walls provide greater energy efficiency, more comfort for the facilities and more security because they are fire resistant.
Regarding greater cost efficiency , they pointed out that the repetitive application of modules allows economies of scale to be exploited, resulting in a reduction in costs both in production and assembly. “There is more predictability, what is reduced are the unforeseen events,” the group indicates.
In turn, the use of exposed concrete walls , both internally and externally, with integrated electrical installations, “significantly optimizes construction times and reduces associated fixed costs.”
Users say the main advantages are greater energy efficiency because the walls that make up the structure combine concrete and expanded polyethylene, which offers “superior thermal insulation”; greater comfort because the panels are produced taking into account all the electrical, sanitary and gas installations, so when installing these devices there is no need to make extra holes; and also greater security because concrete is a highly fire-resistant material.
www.buysellba.com
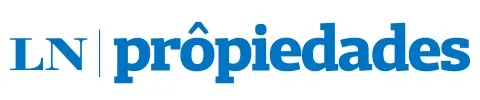
Source:

Cómo es el primer condominio residencial en premoldeado de hormigón del país
Las placas son un desarrollo de un grupo constructor local de la provincia de Córdoba; el sistema reduce hasta 70% los tiempos de ejecución y los costos asociados son más previsibles

October 08, 2024
The plates are a development of a local construction group in the province of Córdoba; the system reduces execution times by up to 70% and the associated costs are more predictable.
By Gabriela Origlia
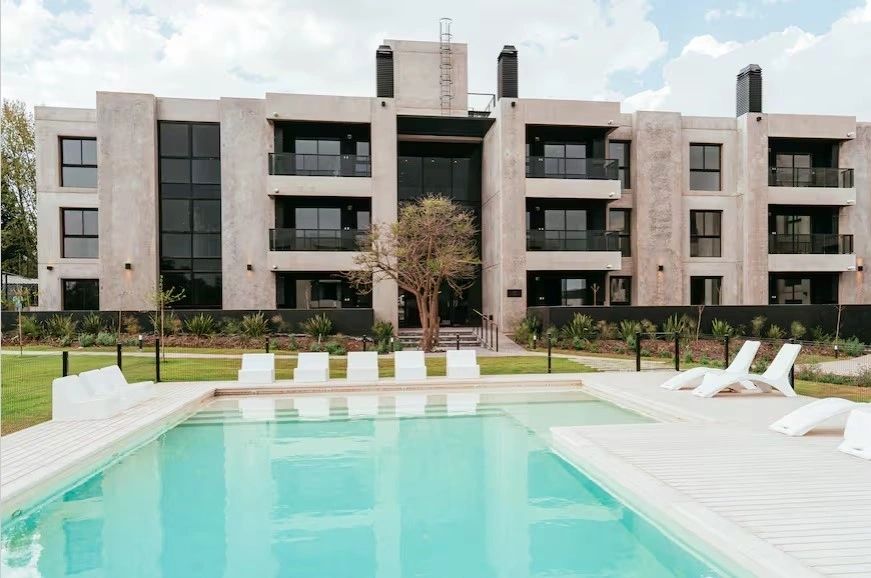
The project in Córdoba will have 10,000 square meters on a 14,000 m2 plot.
CORDOBA.- A real estate development built with precast concrete inaugurated in the northern area of the city of Córdoba , became the first residential condominium in the country built entirely with this technology that reduces construction times by up to 70% while costs have “greater predictability.”
The Garderie residential development has 78 one- and two-bedroom units , ranging from 90 to 110 m², plus a garage; it was designed by the Córdoba-based developer Meade-Pucheta, while the precast concrete is manufactured by Grupo Astori. The walls, load-bearing elements, stairs, floors, beams and columns are industrialized under processes certified with Iso-Iram standards.
Precast concrete is transported from the factory to the construction site and installed so quickly that it significantly reduces the time compared to traditional methods . “The development of this system required us to go beyond what was known, to work meticulously on every detail and to offer an innovative product that responds to the demands of efficiency in construction . We believe that it will revolutionize the construction industry in Argentina,” says María Pía Astori , president of Grupo Astori.
The development has amenities such as a swimming pool, two barbecue areas, as well as a surveillance system and security cameras. Martin Dahan , director of Meade-Pucheta, points out that it is an opportunity for both those who want to live there and for investors .
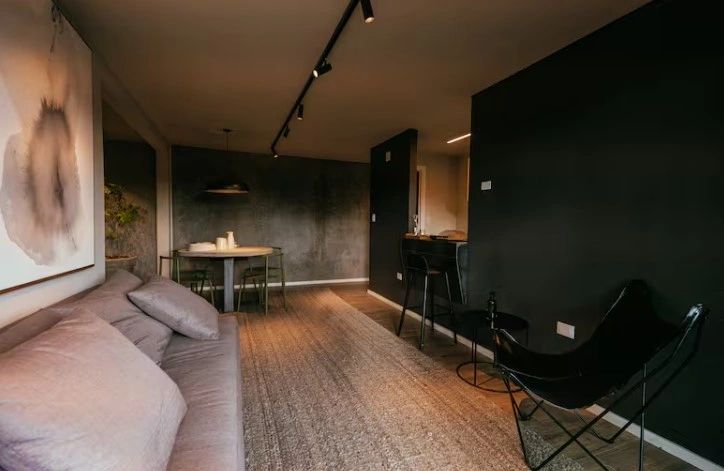
There are apartment walls that maintain the concrete slabs unchanged.
The construction system is a development by the Cordoba group, the result of “exhaustive research” on what exists internationally. They indicated that they studied models in countries with extreme climates, where thermal insulation is essential . These inspired them to design their “sandwich panels, a combination of concrete, expanded polystyrene and a structural mesh .”
The system was adapted to market conditions in Argentina and a methodology was developed that allows for efficient manufacturing in its industrial plants in Córdoba and Buenos Aires, “maintaining a balance between quality, design, and costs, so that the product is highly competitive.”
For each project, the pieces are custom-made to suit the architectural and functional requirements. The construction company explains that the solution is “specifically designed for real estate developments such as housing, buildings, condominiums, collective housing and similar projects.”
In the case of the project in Córdoba, a tower was completed in eight months: the structural part took 60 days and the rest of the work 180 days. This time is equivalent to assembling an entire apartment in just three days. The largest panel used on the façade is a single piece measuring 12 metres high by three metres wide, spanning three floors; it is placed in a single movement, structuring the building and, at the same time, assembling the bedroom closets.
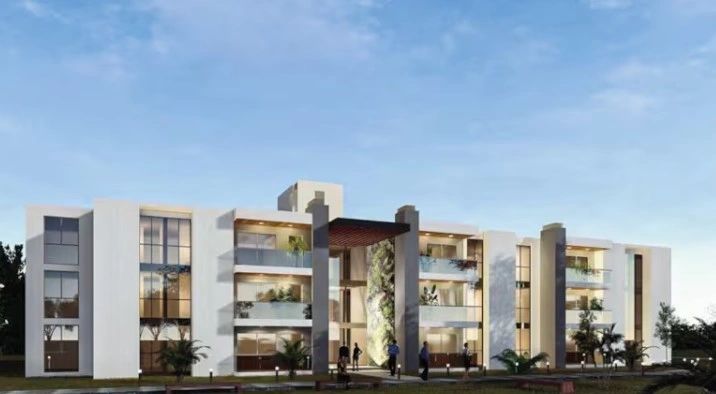
Concrete walls provide greater energy efficiency, more comfort for the facilities and more security because they are fire resistant.
Regarding greater cost efficiency , they pointed out that the repetitive application of modules allows economies of scale to be exploited, resulting in a reduction in costs both in production and assembly. “There is more predictability, what is reduced are the unforeseen events,” the group indicates.
In turn, the use of exposed concrete walls , both internally and externally, with integrated electrical installations, “significantly optimizes construction times and reduces associated fixed costs.”
Users say the main advantages are greater energy efficiency because the walls that make up the structure combine concrete and expanded polyethylene, which offers “superior thermal insulation”; greater comfort because the panels are produced taking into account all the electrical, sanitary and gas installations, so when installing these devices there is no need to make extra holes; and also greater security because concrete is a highly fire-resistant material.
www.buysellba.com