BuySellBA
Administrator
Wooden houses are becoming established in private neighbourhoods: how they are built and what the costs are - Infobae
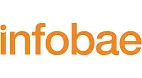
Source:
August 21, 2024
Construction with dry systems such as wood frame is gaining ground in suburban real estate market projects, driven by young families who are opting for sustainable and efficient housing.
By Jose Luis Cieri
Before designing a wood frame home within a private neighborhood, it is important to walk around the lot and know the building codes of each development.
The construction of wooden houses is gaining more and more ground among those who are looking for a home with a sustainable focus and who are opting for dry construction systems. This trend is increasingly reflected in private neighbourhoods where young families are promoting the construction of three or four-room properties in which wood is the absolute protagonist.
"It is a segment in the process of sustained growth, despite the difficulties," explained Daniel Vier , president of the Argentine Chamber of Wood (Cadamda), to Infobae.
Until a few years ago, wood was not considered a relevant construction material in Argentina and was mainly used for decorative elements or in rural constructions. However, Vier highlighted how that trend has changed amid the need to build more efficient and sustainable homes.
Among the types of wood construction systems, wood frame is making progress , a technique in which both profiles and structural plates made of this material are used.
Young families opt for this system because they understand that they gain time because the construction period is shorter and they also reduce costs.
One of the model cases is the San Matías neighborhood in Escobar, where a 100% wooden house is being built with a multi-laminated beam of exceptional dimensions. The work is being carried out by Maderera Newton with the support of Cadamda, with the aim of showing how construction with this material is a sustainable and safe alternative for building, expansion and remodeling.
This is a single-family home of approximately 350 square meters of covered area. The incorporation of 4x20 meter multi-laminated beams stands out in this work, which are not only notable for their dimensions, but also for their support capacity in critical areas.
“In the front of the barbecue area, with a support of 7 meters, they provide a solid and stable structure, combining functionality and aesthetics. In the living-dining area, the 4x20 laminated beams, with a support of 6.20 meters, support the structure of the mezzanine, guaranteeing safety and durability,” commented Vier.
Wooden beams are key to supporting the weight of the house
Local costs range from USD 800 to USD 2,500 per m2, depending on quality and features.
In this regard, Germán Gómez Picasso , from Reporte Inmobiliario, stated: “A few years ago, no wood frame style houses were seen under construction in gated communities; today it can be estimated that at least one or two out of every hundred are of this type of construction.”
Another construction system used is the Wooden Frame , which begins with horizontal surfaces on which the vertical frames are fixed, quickly assembling the envelope to then work on installations and finishes.
Plates are used to insulate the house from the effects of the weather.
There is also the system based on SIP panels ( Structural Insulated Panels ) which consist of two wooden plates joined by a core of rigid foam made of high-density polystyrene or polyurethane, being structurally more solid than masonry and capable of resisting up to 18 tons of compressive load. These panels, suitable for floors, walls and ceilings, are appropriate for buildings, residences and businesses.
The wood frame system , which is used in 90% of homes in countries in the northern hemisphere and the one used in San Matías and in more than 500 homes built in other urbanizations such as El Sosiego, Altos del Carmen, Nordelta, among others, is even more consistent in its use as CLT (Cross Laminated Timber ), as used throughout the world for skyscrapers and buildings of more than 25 floors, especially in countries such as Sweden, Finland, the Netherlands and Denmark, among others.
Due to its ecological and sustainable properties, as well as its thermal characteristics, it is increasingly used in Canada, the United States and much of Europe.
A house of more than 100 m2 takes between 3 and 6 months of construction.
“These generally include everything from aesthetic parameters, minimum and maximum limits that must be met in m2, height, setbacks, among others, to logistical issues, schedules, insurance and documentation to be presented,” explained Eduardo Serantes , commercial manager of B3.
The kitchen of a house in a gated community (Photo Courtesy: B3)
For all these reasons, when starting a preliminary project in a gated community, the first thing builders do is read the regulations and become familiar with all the restrictions and permits to be considered.
Serantes said that “a house of 125 m2 covered is built from the earthwork to delivery in about 3 months and costs between USD 87,000 and USD 113,000. The gap is wide due to the type of finishes, design, number of openings and location.”
The value of the m2 of the house will also depend on the finishing materials that are added in kitchens, bathrooms and living rooms.
The wood frame system has advantages such as speed of construction, reduced costs and lower environmental impact compared to traditional methods, said Serantes.
In addition, it is a cleaner construction, generates less waste and does not raise as much dust. About 6 people work on the assembly of a house, starting with the movement of soil, followed by the foundations, beams and the structure of walls and roof.
Overcoming cultural resistance is the main challenge for the wood sector. But little by little they notice that people are beginning to prefer dry constructions instead of those made in the traditional format.
In Argentina, wood frame homes typically use treated pine or eucalyptus wood laid on 2x4 or 2x5 inch slats.
“The structure is reinforced with OSB panels (Oriented Standard Board in English, which are boards made up of several layers of wood chips joined by glues or synthetic adhesives and then pressed) and internal and external insulating layers are added to ensure great thermal insulation. These houses achieve type A energy efficiency,” Serantes concluded.
www.buysellba.com
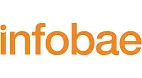
Source:
August 21, 2024
Construction with dry systems such as wood frame is gaining ground in suburban real estate market projects, driven by young families who are opting for sustainable and efficient housing.
By Jose Luis Cieri
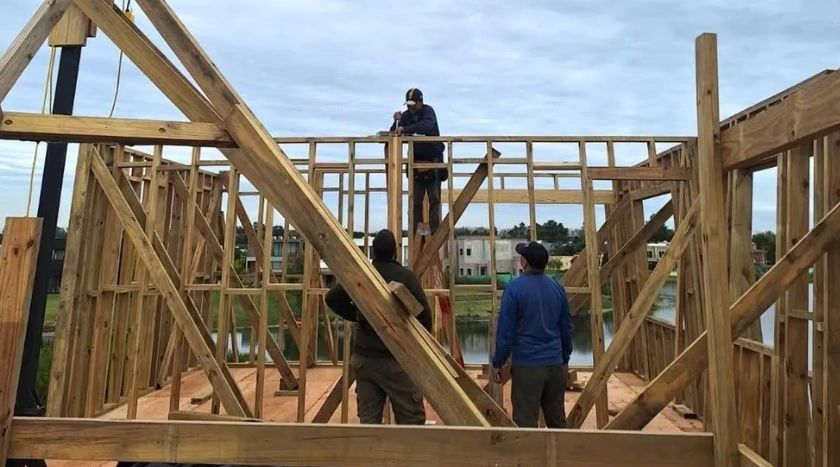
Before designing a wood frame home within a private neighborhood, it is important to walk around the lot and know the building codes of each development.
The construction of wooden houses is gaining more and more ground among those who are looking for a home with a sustainable focus and who are opting for dry construction systems. This trend is increasingly reflected in private neighbourhoods where young families are promoting the construction of three or four-room properties in which wood is the absolute protagonist.
"It is a segment in the process of sustained growth, despite the difficulties," explained Daniel Vier , president of the Argentine Chamber of Wood (Cadamda), to Infobae.
Until a few years ago, wood was not considered a relevant construction material in Argentina and was mainly used for decorative elements or in rural constructions. However, Vier highlighted how that trend has changed amid the need to build more efficient and sustainable homes.
Among the types of wood construction systems, wood frame is making progress , a technique in which both profiles and structural plates made of this material are used.
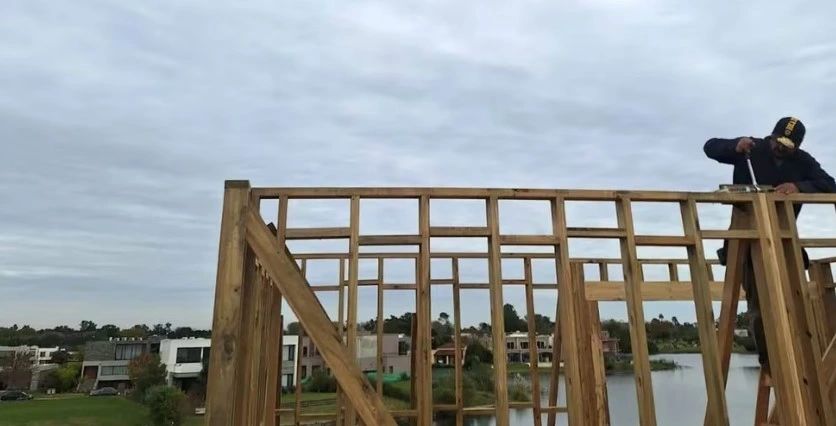
Young families opt for this system because they understand that they gain time because the construction period is shorter and they also reduce costs.
One of the model cases is the San Matías neighborhood in Escobar, where a 100% wooden house is being built with a multi-laminated beam of exceptional dimensions. The work is being carried out by Maderera Newton with the support of Cadamda, with the aim of showing how construction with this material is a sustainable and safe alternative for building, expansion and remodeling.
This is a single-family home of approximately 350 square meters of covered area. The incorporation of 4x20 meter multi-laminated beams stands out in this work, which are not only notable for their dimensions, but also for their support capacity in critical areas.
It has superior thermal insulation with cellulose projected on 5-inch walls, complemented by a ventilated façade that improves energy efficiency, sustainability and interior comfort.
“In the front of the barbecue area, with a support of 7 meters, they provide a solid and stable structure, combining functionality and aesthetics. In the living-dining area, the 4x20 laminated beams, with a support of 6.20 meters, support the structure of the mezzanine, guaranteeing safety and durability,” commented Vier.
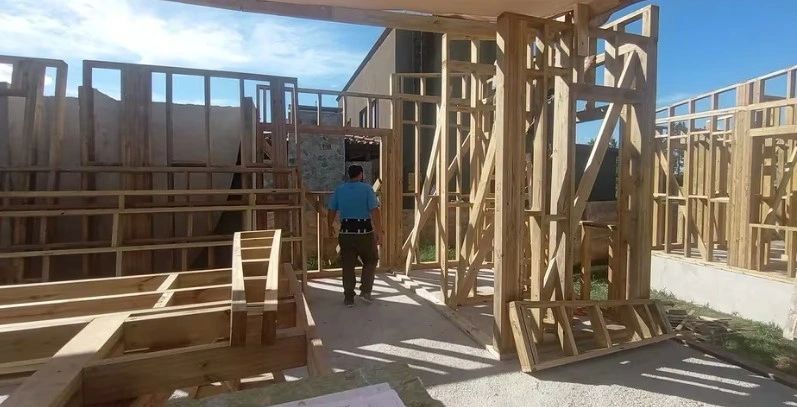
Wooden beams are key to supporting the weight of the house
Local costs range from USD 800 to USD 2,500 per m2, depending on quality and features.
Expansion
Especially in gated communities and gated communities, its use is increasing because it is more resistant to fire. Despite the erroneously established myth, it is crucial to understand the behavior of the home in a fire, since almost all the furniture is combustible and can occur in any type of building. Wood is safer in fires than other commonly used construction materials, it begins to burn from the outside in (this means that despite being on fire it maintains its structural function giving time for rescue). In addition, it has less environmental impact than steel.In this regard, Germán Gómez Picasso , from Reporte Inmobiliario, stated: “A few years ago, no wood frame style houses were seen under construction in gated communities; today it can be estimated that at least one or two out of every hundred are of this type of construction.”
Another construction system used is the Wooden Frame , which begins with horizontal surfaces on which the vertical frames are fixed, quickly assembling the envelope to then work on installations and finishes.
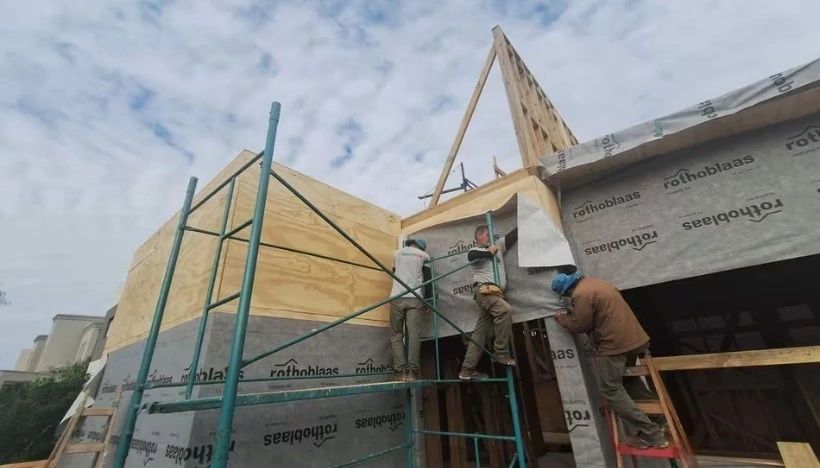
Plates are used to insulate the house from the effects of the weather.
There is also the system based on SIP panels ( Structural Insulated Panels ) which consist of two wooden plates joined by a core of rigid foam made of high-density polystyrene or polyurethane, being structurally more solid than masonry and capable of resisting up to 18 tons of compressive load. These panels, suitable for floors, walls and ceilings, are appropriate for buildings, residences and businesses.
The wood frame system , which is used in 90% of homes in countries in the northern hemisphere and the one used in San Matías and in more than 500 homes built in other urbanizations such as El Sosiego, Altos del Carmen, Nordelta, among others, is even more consistent in its use as CLT (Cross Laminated Timber ), as used throughout the world for skyscrapers and buildings of more than 25 floors, especially in countries such as Sweden, Finland, the Netherlands and Denmark, among others.
Due to its ecological and sustainable properties, as well as its thermal characteristics, it is increasingly used in Canada, the United States and much of Europe.
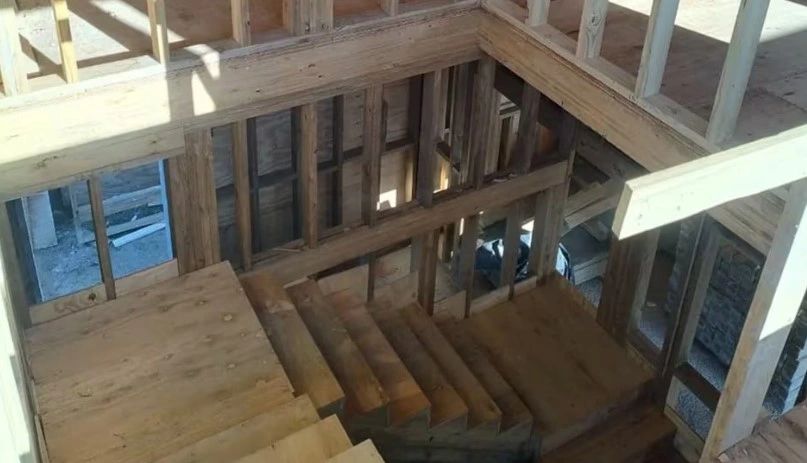
A house of more than 100 m2 takes between 3 and 6 months of construction.
Steps and prices
To build a wood frame home within a private neighborhood, from planning to completion, each development has building regulations that establish aesthetic guidelines, surface and height limits, setbacks, logistical issues, schedules, insurance and required documentation that must be analyzed in detail.“These generally include everything from aesthetic parameters, minimum and maximum limits that must be met in m2, height, setbacks, among others, to logistical issues, schedules, insurance and documentation to be presented,” explained Eduardo Serantes , commercial manager of B3.
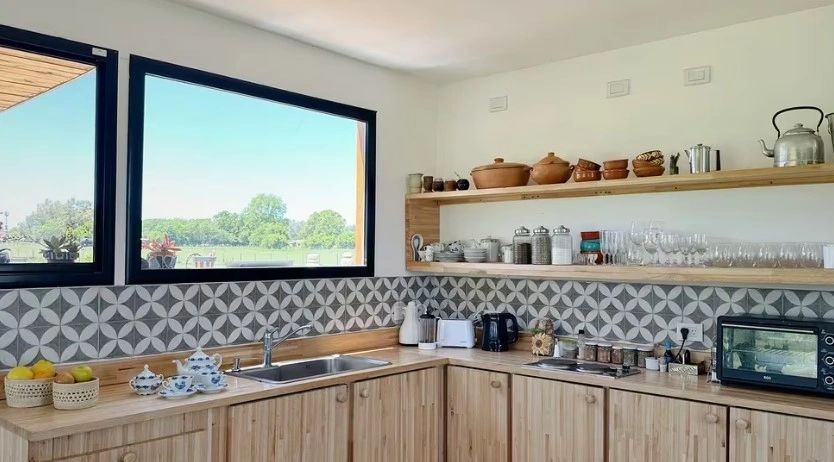
The kitchen of a house in a gated community (Photo Courtesy: B3)
For all these reasons, when starting a preliminary project in a gated community, the first thing builders do is read the regulations and become familiar with all the restrictions and permits to be considered.
Serantes said that “a house of 125 m2 covered is built from the earthwork to delivery in about 3 months and costs between USD 87,000 and USD 113,000. The gap is wide due to the type of finishes, design, number of openings and location.”
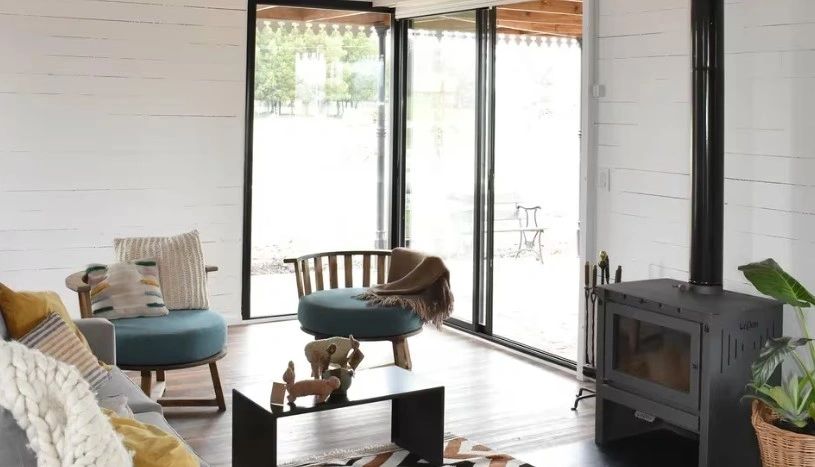
The value of the m2 of the house will also depend on the finishing materials that are added in kitchens, bathrooms and living rooms.
The wood frame system has advantages such as speed of construction, reduced costs and lower environmental impact compared to traditional methods, said Serantes.
In addition, it is a cleaner construction, generates less waste and does not raise as much dust. About 6 people work on the assembly of a house, starting with the movement of soil, followed by the foundations, beams and the structure of walls and roof.
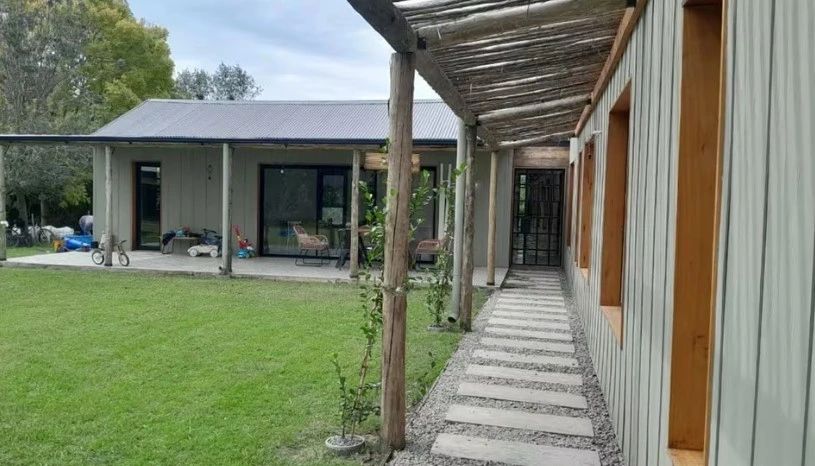
Overcoming cultural resistance is the main challenge for the wood sector. But little by little they notice that people are beginning to prefer dry constructions instead of those made in the traditional format.
In Argentina, wood frame homes typically use treated pine or eucalyptus wood laid on 2x4 or 2x5 inch slats.
“The structure is reinforced with OSB panels (Oriented Standard Board in English, which are boards made up of several layers of wood chips joined by glues or synthetic adhesives and then pressed) and internal and external insulating layers are added to ensure great thermal insulation. These houses achieve type A energy efficiency,” Serantes concluded.
www.buysellba.com